ERP For Manufacturing
Manufactures, Traders, Suppliers
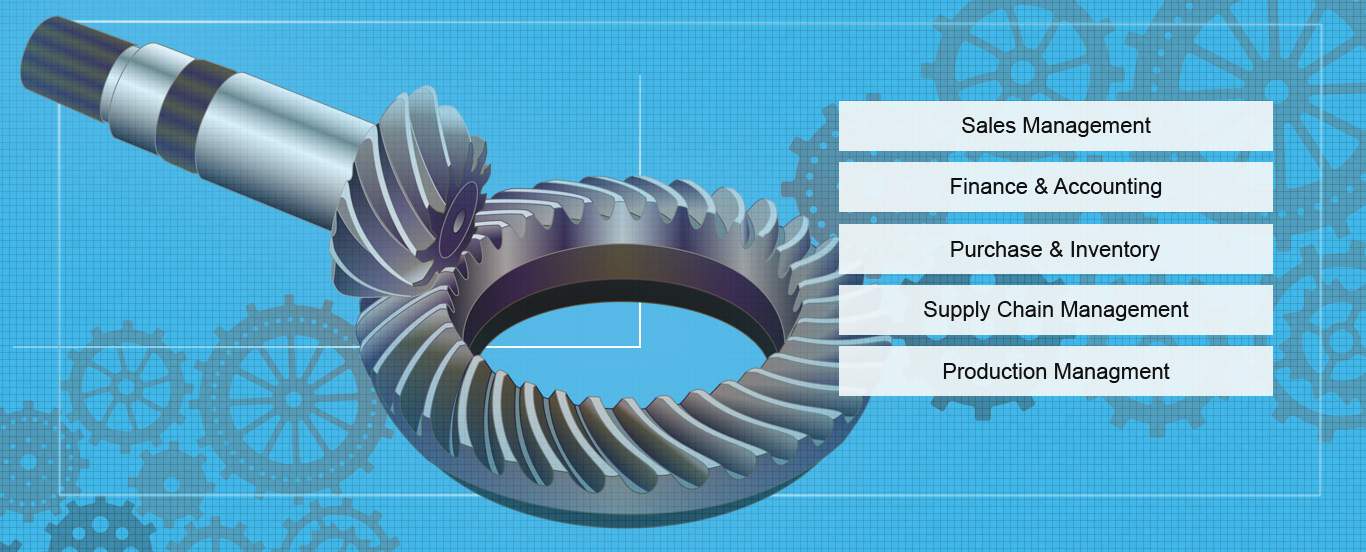
Manufacturing ERP Software
MRP Based ERP for Manufacturers is an integrated management of core business processes, real-time technologies to ensure an efficient and fully customized solution.
The core business activities that ERP covers:
- Product Planning, Purchase
- Production Planning
- Manufacturing or Service Delivery
- Pre Sales & Sales
- Materials Management
- Inventory Management
- Retail
- Logistics & Payment
- Finance
ERP typically offers following advantages:
Operates in real time
Central data repository to support all departments
Excellent Users' interface to provide consistent look and feel across all modules
Browser based and Single Server Installation to minimize maintenance costs
Following common functional areas have been grouped together as one stop solution:
- Finance & Accounting (GST Enabled):
- General Ledger, fixed assets, payables including vouchering, matching and payment, receivables cash management and collections, financial consolidation.
- Management Accounting: Forecasting, budgeting, costing, cost management.
- Human Resources: Recruiting, training, payroll, benefits, appraisal, leave management.
- Manufacturing: Bill of quantities, Job cards or Job work orders, production processes production scheduling as per delivery commitments, machines' capacity and quality control.
- Order Processing: Order to cash, order entry, credit checking, pricing, inventory, dispatch and sales reporting.
- Supply Chain Management: Supply chain planning, supplier scheduling, product configurator, order to cash, purchasing, inventory, warehousing (Receiving, Picking and Packing).
- Project Management: For companies having production with installation & commissioning as a part of their business, will have added features to take Project planning as an integral part of ERP. It will offer resource planning, project costing, work breakdown structure, billing, time and expense, performance units, activity management.
- Customer Relationship Management:
- ERP offers Pre/Post Sales CRM as an integral part of full solution. It takes care of marketing, commissions, service, customer contact, call centre support to constitute a part of Business Support systems.
- Data Services: Another value addition that ERP offers is integrate all employees, vendors & clients through cloud hosted modules.
Manufacturing ERP Modules:
- CRM (Customer Relationship Management)
- Cost & Estimation
- Sales Management
- Import/Export Management
- Project Management
- Purchase
- Inventory
- Warehouse
- Production
- Job Work (Third Party Outsourcing)
- Quality Control
- Calibration
- Distribution Management
- Service Management
- SRM (Supplier Relationship Management)
- SCM (Supply Chain Management)
- Award Management
- Asset Management
- Finance & Accounting
- Taxation
- HR & Payroll
- EPM (Employee Performance Management)
- ESS (Employee Self Service)
- Event Management
- Electronic Data Interchange
- Software Administration
Implementation of ERP
It is important to understand that getting any ERP software implementation means it will bring significant changes to staff work habits and practices.
To ensure the successful implementation, NASTECHS normally starts with consulting with stake holders and SRS development, developing functional and technical documents followed by customization, and finally undertaking users' support round the year.
It is always argued that implementation time is too long and parties tend to delay the implementation.
NASTECHS has the opinion and seriously suggest all stake holders to first ensure that all documents are created and ERP delivery scope has been agreed.
It is also true that time of implementation would change as it depends on number of units in business, number of modules included in ERP scope,
required amount of customization, and the readiness of the users at customer end.
Process preparation before Implementing
Implementing ERP for manufacturing industry requires some ground work to be done in existing business processes. Good understanding of needed process needed prior to starting implementation. Some difficulties may arise due business process, training, or lack of motivation. It becomes therefore vital that organizations either to undertake some SOP audit (Standard Operating Procedures) or thoroughly analyse and refine processes before they implement ERP.
NASTECHS highly recommends organizations to consider some kind of SOP is undertaken in order to make decentralized management. As some business rules, data semantics, authorization hierarchies, and decision Centre spoil the chances of a successful ERP implementation.
Configuration
Configuring an ERP system is largely a matter of balancing the way the organization wants the system to work around them rather than they work around the ERP system.ERP includes many settings that modify system operations such as selection of the type of inventory accounting,
FIFO or LIFO or Weighted Average.
Other Advantages:
Technology Platform and Cyber Security
Post Implementation Support